When standard enclosures don’t meet your project’s unique requirements, customization is the best solution. Whether you need a plastic or aluminum waterproof junction box, an aluminum extrusion enclosure, a plastic or aluminum tool case, or a custom electrical box, tailored designs ensure optimal performance, durability, and aesthetics.
This comprehensive guide explores how to customize different types of enclosures, including material choices, dimensions, colors, perforations, mounting plates, and additional features like foam inserts.
1.Customizing Plastic Waterproof Junction Boxes
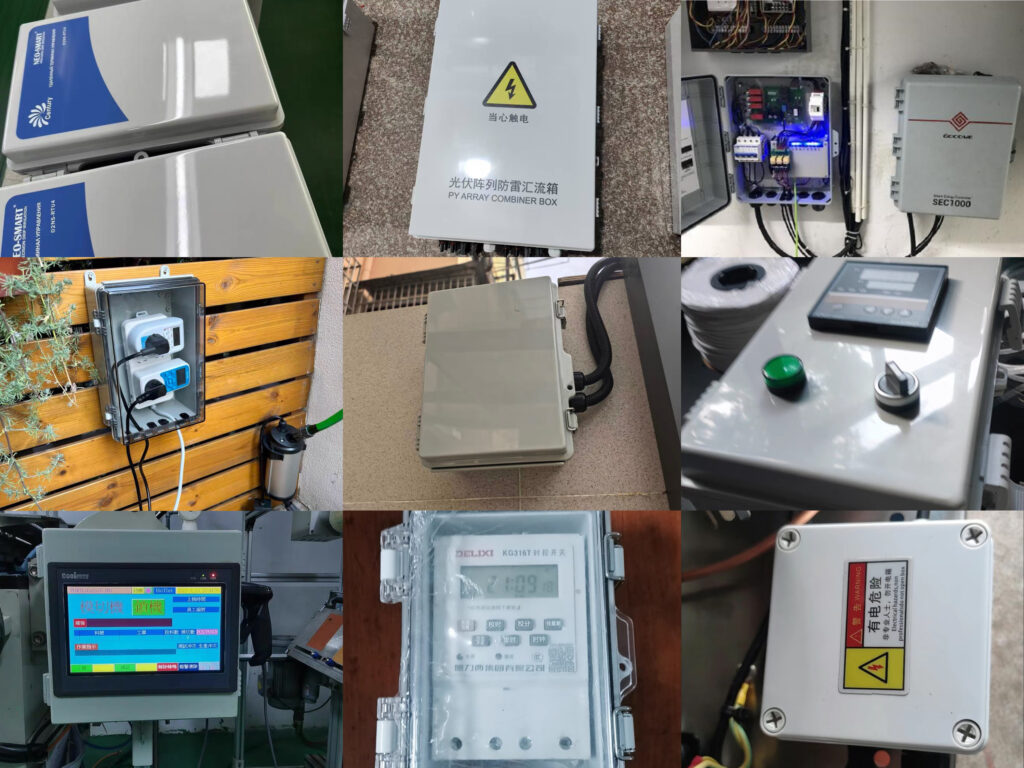
Waterproof junction boxes are ideal for outdoor, marine, and industrial applications where moisture resistance is crucial. Here’s how to customize them:
- Material Selection
Performance Requirements: Select plastic materials with appropriate performance characteristics based on the operating environment and functional requirements of the junction box. For example, in high-temperature environments, choose materials with high-temperature resistance; in humid environments, select moisture-resistant and waterproof materials.
Material Types: Common materials include polycarbonate (PC), which offers high strength, high transparency, and excellent weather resistance; polyvinyl chloride (PVC), which is cost-effective and has good insulation properties; and acrylonitrile-butadiene-styrene copolymer (ABS), which has excellent overall performance and is easy to process and form.
Additive Applications: To enhance specific material properties, various additives can be incorporated, such as flame retardants to improve fire resistance, UV stabilizers to enhance weatherability, and impact modifiers to improve material toughness.
- Customize Color
Color selection: Customers can choose from a variety of colors based on their brand image, usage environment, or personal preferences. Common colors include basic colors such as white, gray, and black, as well as vibrant warning colors such as red and yellow, which are used in special situations to attract attention.
Color customization: For customers with specific color requirements, precise color matching can be achieved by blending color masterbatches to ensure that the customized color matches the color sample provided by the customer.
- Hole Drilling
Hole Position Design: Based on the application scenario of the junction box and customer requirements, the positions of the holes are precisely planned. For example, to accommodate the wiring of specific equipment, it may be necessary to drill holes of varying numbers and spacings on the sides, bottom, or top of the box.
Hole Diameter: Customize the hole diameter based on the diameter of the connected wires or cables. Common hole diameters range from a few millimeters to several dozen millimeters to ensure smooth wire passage while maintaining good sealing performance.
Hole Shape: In addition to standard round holes, holes can be designed in shapes such as square or elliptical to accommodate different types of connectors or installation methods.
- Custom logo
Logo design: Based on the brand identity or design concept provided by the customer, the logo is digitally designed to ensure clarity and accuracy for precise reproduction on the junction box.
Printing Processes: Options include screen printing, heat transfer printing, and laser engraving. Screen printing is cost-effective for simple logos with limited colors and shapes; heat transfer printing offers vibrant color effects; laser engraving provides permanent and high-precision results, ideal for applications requiring logo durability.
Position and Size: Determine the printing position of the logo based on the overall appearance of the junction box and customer requirements, such as the front, side, or bottom of the box cover. Additionally, adjust the size of the logo appropriately based on the dimensions and visual impact of the junction box to ensure it stands out without compromising the overall aesthetic appeal.
- Customized mounting plates or rails
Customized mounting plates: Design mounting plates of different sizes and shapes according to the installation requirements of the equipment. Honeycomb plates are available for selection. Various mounting holes, slots, or screw columns can also be customized to secure the junction box to specific equipment or panels. The material of the mounting plate can be the same as or different from the junction box body, and its strength and stability must be considered.
Rail Customization: For junction boxes that need to be installed on rails, a suitable rail structure must be customized. The shape, size, and material of the rail must match standard electrical installation rails to ensure the junction box can be securely mounted on the rail and easily removed or replaced. Additionally, the electrical connection performance between the rail and the junction box must be considered to ensure proper grounding, etc.
2. Customizing Aluminum Waterproof Junction Boxes
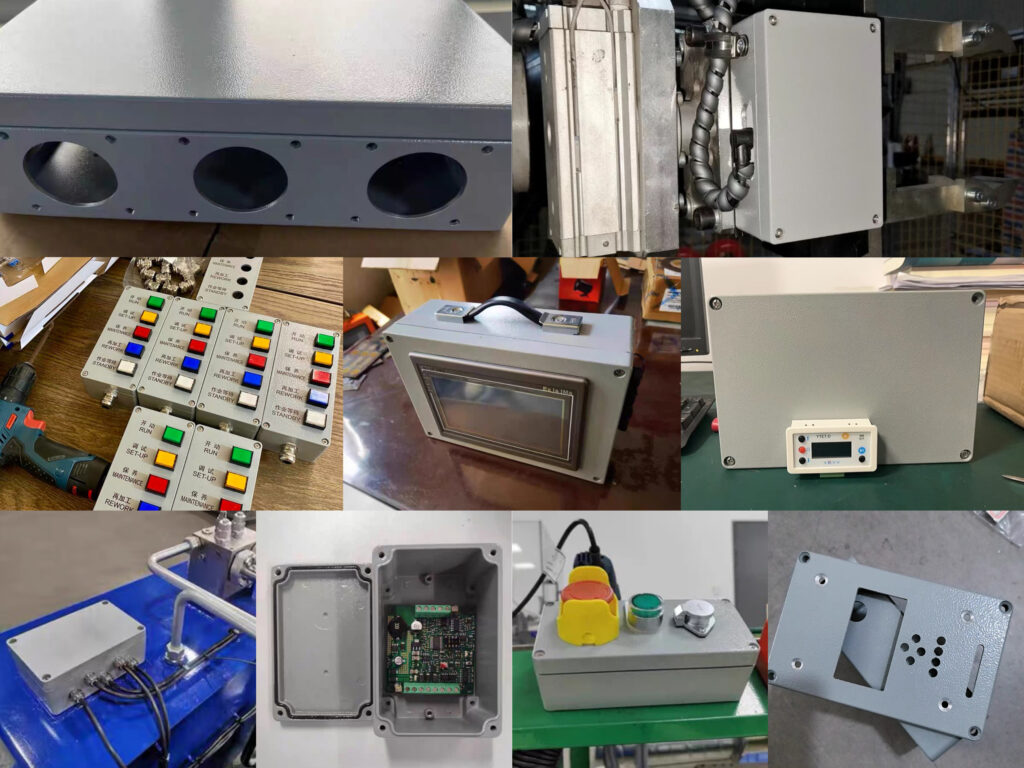
Aluminum waterproof box offer superior heat dissipation, EMI shielding, and ruggedness. Customization options include:
- Color & Finish
Our standard color is industrial gray, and customers can choose colors that match their brand from the RAL or Pantone color charts. We can achieve custom colors by mixing liquid or powder coatings.
Surface treatments are typically anodizing and powder coating. Anodized oxide films are hard and wear-resistant, effectively protecting the surface of aluminum waterproof boxes. Powder coating offers a wide range of colors and has good corrosion resistance, wear resistance, and chemical resistance. It also has good environmental performance.
- Custom Holes
Mechanical drilling: Suitable for processing holes of various shapes and sizes, especially for conventional holes where precision requirements are not particularly high. It is widely applied in single-piece or small-batch production, such as drilling installation holes on aluminum waterproof boxes for small electrical devices.
Laser drilling: Suitable for processing high-precision, small-diameter holes, such as those required in high-performance electronic equipment aluminum waterproof boxes. It is also suitable for mass production of aluminum waterproof boxes, enabling efficient and rapid processing. For example, in the production of standardized electrical product aluminum waterproof boxes, it is used to process regular installation holes or cable exit holes, as well as heat holes or tiny cable exit holes. Additionally, for special-shaped holes such as irregular holes or micro-holes, laser drilling offers significant advantages.
Stamping drilling: Suitable for mass production of aluminum waterproof boxes, enabling efficient and rapid processing. For example, in the production of standardized electrical product aluminum waterproof boxes, it is used for processing regular installation holes or cable exit holes.
- Mounting Plates & Rails
Based on the internal space of the aluminum junction box and the size requirements of the customer’s installed equipment, the size and shape of the custom installation plate are determined. It can be a rectangular plate of the same size as the bottom surface of the junction box, or an irregularly shaped plate designed according to the layout of specific electrical components. Installation holes of different specifications and positions are set on the installation plate to accommodate the installation of various electrical components.
Rails are typically secured to the inner walls of the junction box or the mounting plate using screws or slots. For applications requiring frequent replacement of electrical components, removable mounting methods can be used for easy maintenance and replacement; for applications requiring high stability, welding or riveting methods can be used to ensure a secure connection between the rails and the junction box.
3. Customizing Plastic Equipment Case
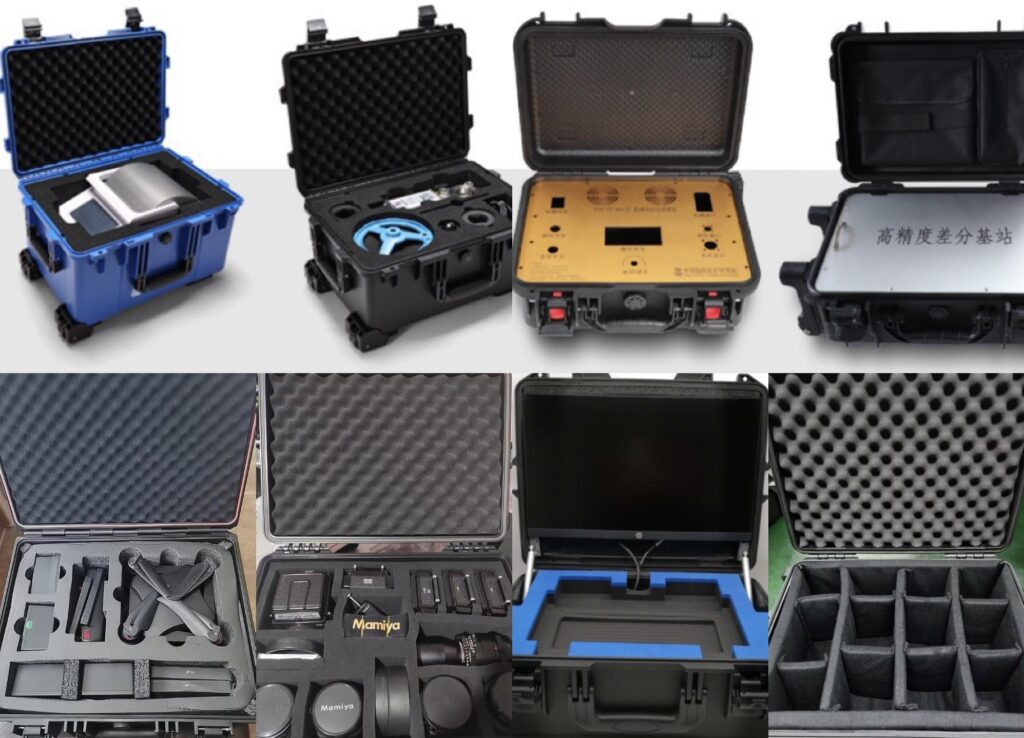
Plastic equipment case are used in used to safeguard various items from physical damage, environmental factors, and theft, etc. It is applied in military, medical, industrial, outdoor and other fields. Custom features include:
- Custom Color and Logo
Color Customization: Our standard color is black, but we can produce the protective box in the color specified by the customer to match the usage environment or corporate image.
Logo Printing: We can print the customer’s specified logo, text, patterns, etc. on the surface of the protective box, such as company logos, product names, warning signs, etc., to serve as identification and promotion.
- Internal Structure
Compartments and Dividers: Depending on the type and quantity of items to be stored, different compartments, dividers, or slots are set up inside the box to keep items organized and easy to access.
Cushioning Materials: Cushioning materials such as sponge and foam are added inside the box to protect valuable or fragile items from shock.The common types of sponges include PU,EVA and EPE. The foam can be cut according to the customer’s product.
- Custom Holes
Holes can be drilled as needed. To maintain protective performance, waterproof connectors can be used. eg.IP-rated cable entry points.Filtered vents for dustproofing.
- Customized lock
Password locks or padlocks can be customized.
4. Customizing Aluminum Tool Cases
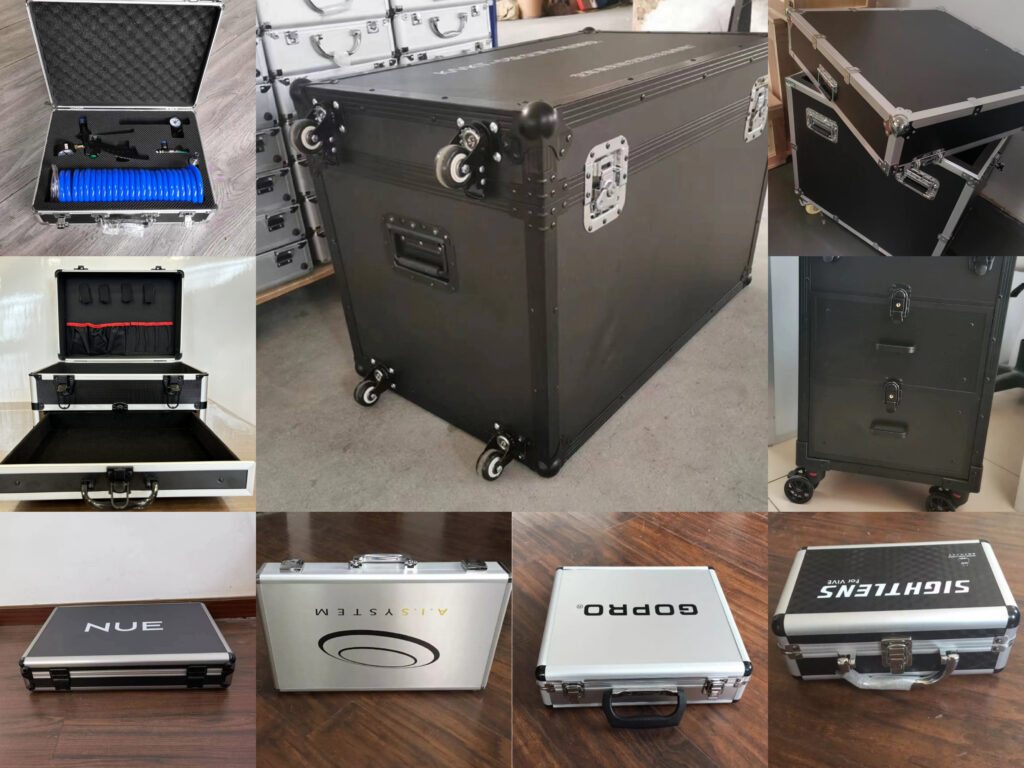
Aluminum tool cases are widely used in industry, aerospace, outdoor, household and other fields.Aluminum box customization typically includes the following:
- Dimensions and Structure
Customized Dimensions: Based on the user’s actual needs, the length, width, and height of the toolbox are determined to accommodate the storage requirements of different tools. For example, toolboxes customized for large professional tools will be larger, while small household toolboxes will be smaller in size.
Internal Structure Design: Different compartments, sections, and slots can be designed based on tool types and usage habits. For instance, specialized long tool slots, small parts storage compartments, and adjustable dividers can be included to facilitate the organized storage of various tools.
- Material and Thickness
Material Selection: Aluminum alloy is generally used. Different aluminum alloy grades can be selected based on the usage environment and performance requirements. For example, 6061 aluminum alloy has high strength and good corrosion resistance, making it suitable for outdoor use.
Panel Thickness: Customized density panel of different thicknesses are available based on the size, load capacity, and usage requirements of the toolbox. For example, thicker sheets can be used for large, heavy-duty toolboxes to ensure the strength and stability of the box.
- Accessory Options
Handles: Choose from plastic handles, metal handles, etc., customized to provide different grip sensations and load-bearing capacities as needed.
Locks: Options include standard padlocks, combination locks, and latch locks to ensure the security of items inside the box.
Casters: Equipped with casters of different materials and specifications, such as silent swivel casters, for easy movement and transportation of the aluminum box.
- Exterior Design
Color Customization: Customize various colors based on brand image or personal preferences to enhance the aluminum box’s distinctiveness.
Logos and Patterns: Add company logos, product identifiers, or other patterns to the aluminum box surface for promotional and aesthetic purposes.
5. Customizing Aluminum Extruded Enclosures
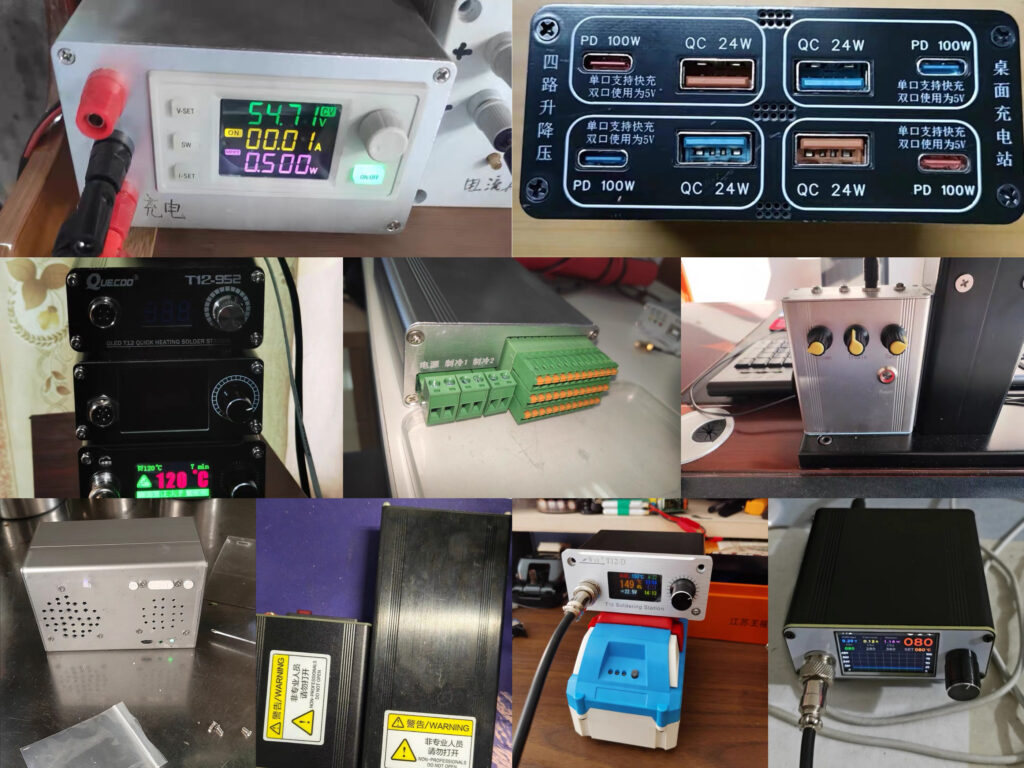
Extruded aluminum enclosures allow for highly modular and scalable designs.The customization of electrical enclosure housings primarily encompasses the following aspects:
- Material
Commonly used is 6063 aluminum alloy, which has good corrosion resistance, machinability, and surface treatment properties, making it suitable for applications with high requirements for appearance and corrosion resistance; 6061 aluminum alloy has higher strength and is often used in products with structural strength requirements.
- Surface treatment
Includes anodizing, which forms a hard, wear-resistant, and corrosion-resistant oxide film and is available in a variety of colors; electrophoretic coating, which produces a uniform, smooth coating with excellent weather resistance and decorative properties; and powder coating, which offers a wide range of colors, thick coatings, and excellent protective properties.
- Customized dimensions
The length, width, height, and dimensions of each part of the aluminum profile enclosure are precisely customized according to the internal structure and installation requirements of the product to ensure a perfect fit with the internal components.
- Custom punching
Various shapes of holes, such as square, round, and irregular shapes, can be punched according to product functions and requirements.
- Customized logo
Screen printing can be used to print the logo on the surface of the aluminum profile with ink, which is rich in color and low in cost. Laser engraving can also be used to engrave the logo on the aluminum profile with a laser beam, which is highly accurate and durable.
6. Customizing Electrical Distribution Enclosures
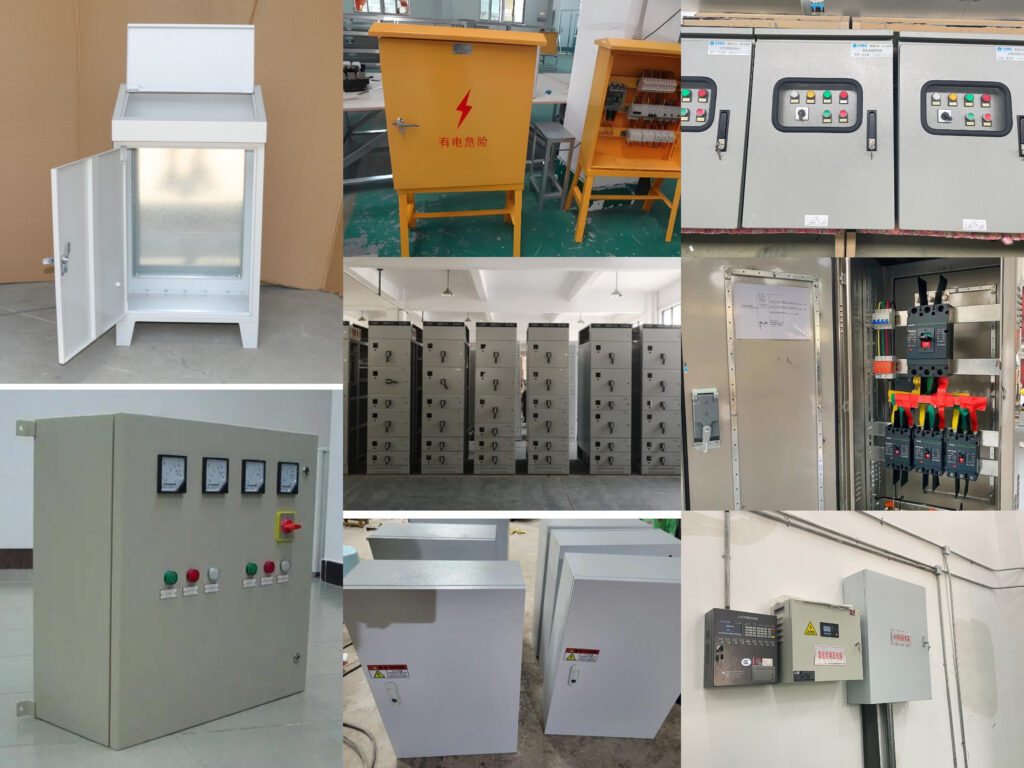
Electrical enclosures house breakers, switches, and control systems. Customization ensures compliance and functionality.
- Specifications and Dimensions
Based on the quantity, size, and layout of electrical components inside the enclosure, custom dimensions for length, width, and height are determined to ensure proper installation of components while facilitating operation and maintenance.
- Material Selection
Considering the operating environment and performance requirements of the electrical enclosure, different materials can be selected. For example, cold-rolled steel plates offer high strength and good machinability, with surfaces that can be powder-coated for rust prevention and corrosion resistance; stainless steel materials provide strong corrosion resistance and are suitable for harsh environments.
- Exterior Design
Color: Typically, classic colors such as gray or its original color are chosen. Custom colors can also be tailored to customer requirements or usage scenarios to meet visual requirements in different environments.
Surface Treatment: Common methods include powder coating and baking paint, which make the exterior surface smooth and aesthetically pleasing while enhancing rust resistance and wear resistance.
- Structural Design
Door Design: Single-door, double-door, or swing-door configurations are available, determined by the size of the electrical enclosure and operational convenience. The door must be securely installed, operate smoothly, and have excellent sealing performance.
Ventilation and Heat Dissipation: Ventilation holes, heat dissipation slots, or cooling fans are designed into the enclosure to ensure effective heat dissipation of electrical components during operation, preventing overheating.
Protection Rating: Different protection ratings, such as IP54 or IP65, are designed based on the usage environment to prevent dust, water, and other contaminants from entering the interior of the electrical enclosure and protecting the electrical components.
- Functional Customization
Mounting Holes: Mounting holes are pre-drilled on the enclosure based on the installation location and fixation method of the electrical components to facilitate their installation and fixation.
Grounding Device: A reliable grounding terminal is provided to ensure safety during use and prevent electrical leakage accidents.
Markings: Clear markings, such as the electrical enclosure’s name, number, and warning symbols, are printed or affixed to the enclosure surface for easy identification and operation.
Conclusion
The advantages of custom enclosures include, but are not limited to, the following
✅ Perfect fit for components
✅ Enhanced protection against environmental factors
✅ Professional appearance with brand-specific colors/logos
Need a custom enclosure? Contact us now for a customized solution!